November 2, 2023
Finland’s largest metal 3D print was tested according to the pressure vessel standard EN 13445-3. The pressure vessel and test results are presented at Formnext Frankfurt.
The pressure vessel realized in cooperation between ANDRITZ Savonlinna Works Oy and the FAME Ecosystem withstood the non-destructive and destructive tests carried out by LUT University better than expected. In the tests, the pressure was increased until the piece started to break. This happened at a pressure of 111 bar.
“This vessel was designed for an operating pressure of 10 bar, which includes the safety factors. The preliminary calculation showed that the rupture would occur at around 90 bar, i.e. the actual durability far exceeded expectations. It must be noted that in real production pieces, the test pressure of the pressure vessel is usually only done at around 1.5 times the operating pressure, i.e. in this case the test pressure would have been only 15 bars,” says Santeri Varis, Additive Manufacturing Manager at ANDRITZ Savonlinna Works Oy.
“It was known in advance that the quality of the method used on a small scale is good, but there was no experience with such a large scale. I was surprised by such a high result, and it certainly strengthened my belief in the good quality of WAAM,” he continues.
The approximately 300-kilogram pressure vessel is manufactured with ANDRITZ Savonlinna Works Oy’s equipment, whose operating principle is direct deposition, arc as an energy source (DED-Arc). Colloquially, the method is known by the abbreviation WAAM (Wire Arc Additive Manufacturing). Made of acid-resistant stainless steel (316L), the approximately 300-kilogram pressure vessel has a diameter of 900 mm and a height of 1600 mm. Elomatic has also been involved in its design phase.
A small fracture next to the leg
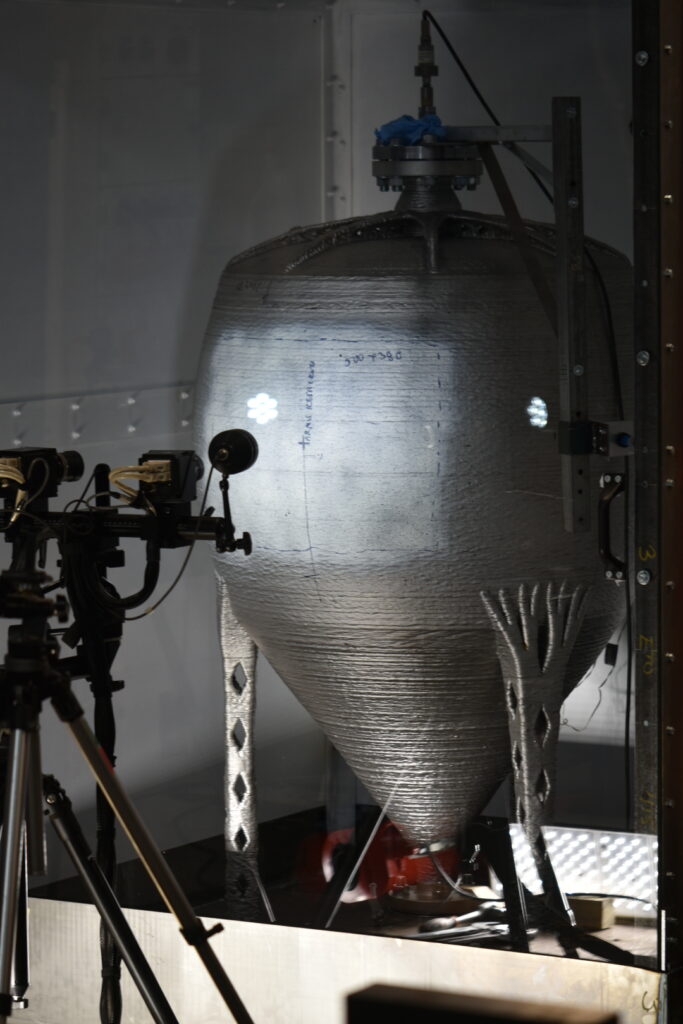
The pressure vessel has been tested in many ways. First, it underwent non-destructive testing (NDT) with penetrant. LUT University’s experiments tested its material and geometry-based performance. The finished part was compared with, among other things, the CAD model, which it matched at best with an accuracy of two millimeters on average, which is a very good result, which is practically explained by the width of the printed weld.
In the pressure test, water was pumped into the vessel, and it was monitored what changes it causes in the diameter of the widest part of the vessel. The pressure was gradually increased at first and finally to the maximum.
“Under 66 bars, there were still no noticeable changes in the vessel. The shape started to give way after 80 bars. We continued the test so long that some water leaked out of the vessel at 111 bars. At that point, a small crack appeared next to the legs of the vessel. The diameter had expanded by seven percent. The result is very good for a piece like this, which is designed to withstand much lower pressure,” says Doctoral Researcher Kalle Lipiäinen from LUT University.
The crack was welded and in the next test there was a fracture right at the leg again. This indicated that the leg area was a structural weak point, and the first breakdown was not due to, for example, a manufacturing error.
There is now information about the use of WAAM in large pieces that was not available before. The FAME Ecosystem distributes information to companies and LUT publishes scientific articles on the subject.
“We learned a lot from the testing process. It would be great if there were more opportunities to carry out tests of large 3D printed parts and hybrid structures,” says Lipiäinen.
Waiting for standards
“The test results show the skeptics that high-quality pieces can be made with 3D printing if you know what to do and understand the design and manufacturing process. Now it’s just a question of companies’ ability to adapt new technology into their own manufacturing processes, because otherwise there’s a risk of falling behind competitors,” says FAME Ecosystem Lead Eetu Holstein from DIMECC Oy.
In Finland, many companies in the metal industry would in principle already have all the prerequisites to manufacture their own 3D printed pressure equipment and other products, because the printing equipment needed for WAAM practically consists of a robotic welding cell and a robotic welding power source, where you can find a program suitable for the WAAM process.
However, a 3D-printed pressure vessel will not immediately appear on the market. The reason for that is standardization. Pressure vessels must meet the pressure equipment directives and EN standardization is at the stage that the working group has been established. This means that in a few years there may be standards for design and production. While waiting for that, the process and testing can be refined.
In the printing of the pressure vessel, the arc time was about 100 hours, but the actual production time, including cooling, inspections and measurements, and learning, was about 300 hours. More than three kilometers of welds were consumed in the pressure vessel. At its best, the printing speed was three kilograms per hour.
The testing of the Finnish skill sample has attracted international interest, so the pressure vessel and the results will be presented in Frankfurt at Formnext, the main event of additive manufacturing.
“In Finland, we have enormously good expertise in the design, manufacture and testing of 3D prints. We are able to stand out in the world as experts in particularly demanding 3D prints, which means demanding designs and applications as well as the ability to print rarer materials. We are trying to bring this message to the attention of people both in Finland and abroad,” says Eetu Holstein.
The pressure vessel and the test results are on display at Formnext’s Nordic Pavilion, hall 11.0, stand D68.
More information
Ecosystem Lead Eetu Holstein, DIMECC Ltd., tel +358 40 840 8660, eetu.holstein@dimecc.com
fame3d.fi