June 22, 2021
HT Laser is a system and component supplier for global machine building companies and a flexible subcontracting partner for forest, paper, energy, marine, mining, and other industries. HT Laser serves in eight cities in Finland and in Poznan, Poland.
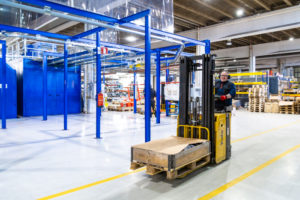
With the help of data management, it is possible to efficiently implement customer-specific packaging requests. Picture: HT Laser Oy
HT Laser offers all cutting, bending, welding, laser welding, machining, surface treatment, 3D metal printing, assembly, and related R&D services.
The information flow related to the material is a key development target in the systematic digitization of HT Laser’s processes and data sharing in the value network. This was targeted in the project HT Laser implemented in DIMECC Industrial Data Excellence – InDEx program.
As part of a larger digitization project of logistics processes, the aim was to develop collection of sheet metal parts related to deliveries and to increase the efficiency of related data transfer both internally and between HT Laser and customer companies.
The advantages and benefits
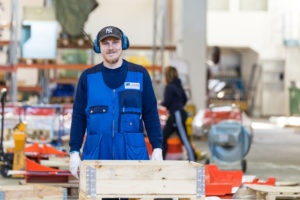
Digital solutions for HT Laser’s logistics operations have been developed in InDEx. Image HT Laser Oy
The sharing of data in the value chain reduces unnecessary mistakes. After the development, information about the desired packing order and packaging is transferred from the customer company’s system to the supplier. As a result, the work of the welder or installer of a company that orders HT Laser sheet metal parts becomes more efficient, since it is possible to pick up the parts needed in the right order straight from the package.
The customer company benefits from the employees not having to spend time on collection and less storage space is needed. For HT Laser, improving the transfer and accessibility of logistics data means improving quality. New visual solutions reduce the need for translations and collection errors for example in multilingual work communities.
“This rapidly implemented pilot is a successful practical example of how digital solutions can be effectively leveraged to share information related to customer needs and improve usability. By making effective use of information, it is possible for us to develop our own operations only to a higher standard and to focus on the most important issues for our customers. We will certainly spread the tools and practices we have now created to other HT Laser units as well,” says Sami Tiikkainen, Vice President and HT Laser Vieremä Unit Manager.